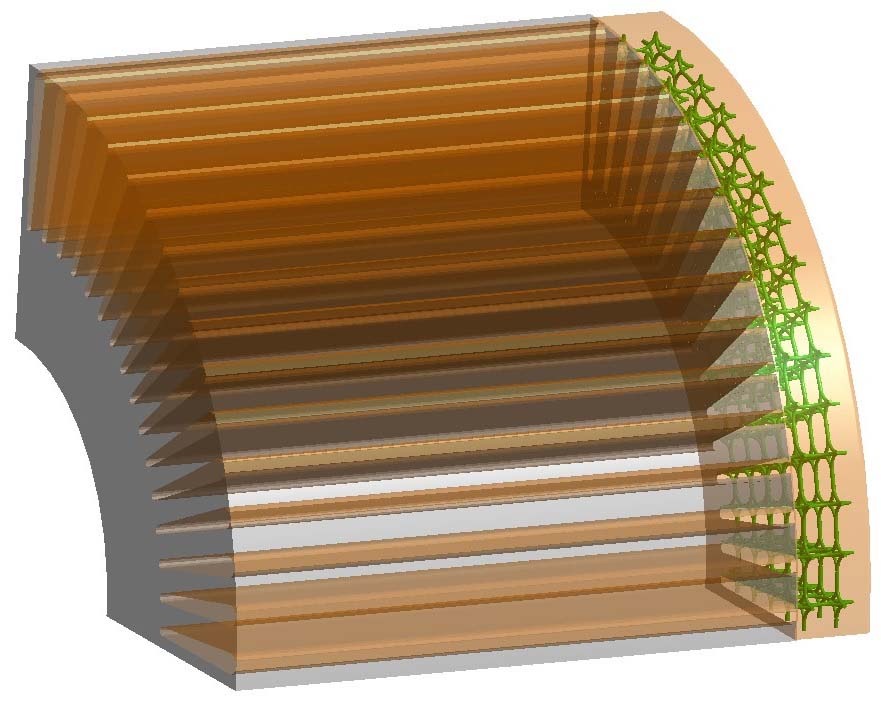
Mehr Ressourceneffizienz bei der Produktion von elektrischen Fahrzeugantrieben
Ein neues Forschungsprojekt untersucht Möglichkeiten zur Kombination von metallischem 3D-Druck und Kupferdruckguss bei elektrischen Maschinen.
Im Forschungsprojekt „Additive Fertigung von Tragstrukturen für ressourceneffiziente elektrische Hochdrehzahl-Asynchronantriebe (ATREA)“ an der Fakultät Elektrotechnik untersuchen Wissenschaftler der Forschungsgruppe Elektrische Maschinen und Antriebe, wie sich der Einsatz energieeffizienter und robuster Asynchronmaschinen mit Käfigläufer auf elektrische Fahrzeugantriebe ausweiten lässt.
Je höher die Antriebsdrehzahl, umso höher ist die Leistungsdichte und damit die Ressourceneffizienz elektrischer Antriebsmaschinen. Bislang wird die Drehzahlfestigkeit durch den Einsatz von zusätzlichen Bandagen oder von hochfesten Legierungen für die Käfigwicklung des Rotors gesteigert. Dies geht allerdings zu Lasten des Wirkungsgrades der Maschine. Im Forschungsprojekt kombinieren die Forscher nun additiv gefertigte Tragstrukturen mit der Technologie des Kupferdruckgusses. „Wir wollen zum einen die additiv gefertigten, festigkeitssteigernden Strukturen in den Kurzschlussring eingießen und zum anderen den Kurzschlussring an einen mittels additiver Verfahren strukturierten Läuferkörper angießen,“ erläutert Prof. Thomas Schuhmann, der Leiter des Projektes.
Weniger Aufwand, größere Materialeinsprung
Neben der Vermeidung aufwändiger zusätzlicher Prozessschritte bei der Aufbringung der Bandage ermöglicht das Verfahren aufgrund der höheren Drehzahlfestigkeit und Leistungsdichte insgesamt eine Materialeinsparung. „Die eingesetzten Ressourcen lassen sich nahezu vollständig recyceln. Das Eingießen der 3D-gedruckten Strukturen gestattet die Verwendung von Legierungen mit höherer elektrischer Leitfähigkeit für die Rotorwicklung und damit auch eine Energieeinsparung beim Betrieb,“ ergänzt Uwe Schuffenhauer, wissenschaftlicher Mitarbeiter im Projekt.
Zunächst sollen geeignete Materialkombinationen aus metallischem 3D-Druck und Kupferdruckguss hinsichtlich ihrer Struktur sowie physikalischer und technologischer Eigenschaften geprüft werden. Dabei müssen neben den strukturmechanischen Grenzen auch die Anforderungen hinsichtlich der elektromagnetischen Materialeigenschaften (insbesondere Magnetisierbarkeit, elektrische Leitfähigkeit) im Aktivteil der E-Maschine berücksichtigt werden. Anschließend legen die Forscher Rotorgeometrien mit Tragstrukturen im Kurzschlussring sowie am Läuferkörper aus und optimieren diese unter elektromagnetischen sowie strukturmechanischen Gesichtspunkten. Der 3D-Druck ermöglicht dabei das Testen von unterschiedlichen Materialien und vielen geometrischen Varianten. So können der Gießprozess und die Eigenschaften der elektrischen Maschine optimiert werden.
Das Teilvorhaben wird mit rund 320.000 € vom Bundesministerium für Wirtschaft und Klimaschutz aus dem „Energie- und Klimafonds“ gefördert. Das Projekt läuft bis Oktober 2024. Projektpartner sind die Breuckmann eMobility GmbH (Heiligenhaus) sowie Oerlikon AM GmbH (Feldkirchen).